At its core, CNC milling entails the elimination of product from a work surface via a collection of worked with motions. When the style is completed, the operator uses computer-aided manufacturing (CAM) software to translate the CAD model right into a collection of directions that the CNC device can check out, generally in the form of G-code.
One of the standout features of CNC milling is its versatility. Unlike traditional milling machines, which typically operate along a couple of axes, CNC milling machines can operate numerous axes all at once-- generally three, four, or perhaps 5. This ability enables producers to achieve extra intricate geometries than ever in the past. For circumstances, a three-axis milling maker can move along the Y, x, and z axes to create a variety of forms, while a five-axis machine can tilt and turn the workpiece, enabling access to hard angles and surfaces. This adaptability not only boosts style opportunities however also enhances the production procedure, as it reduces the demand for multiple arrangements and comprehensive hand-operated interventions.
Check out cnc milling guide the transformative globe of CNC milling, a technology that incorporates precision and automation to create top quality elements efficiently from different products, and discover its procedures, benefits, and essential factors to consider for success in modern production.
The choice of devices is an additional vital facet of CNC milling. There is a wide range of cutting tools readily available, including end mills, face mills, and sphere mills, each suited for different applications. End mills, for instance, are versatile devices that can be made use of for side and face cutting, while sphere mills are excellent for creating complicated contours and spherical corners. The proper device selection can considerably impact the high quality of the ended up product and the effectiveness of the machining procedure. In addition, proper tool upkeep and problem surveillance play a significant function in keeping optimal performance and extending device life.
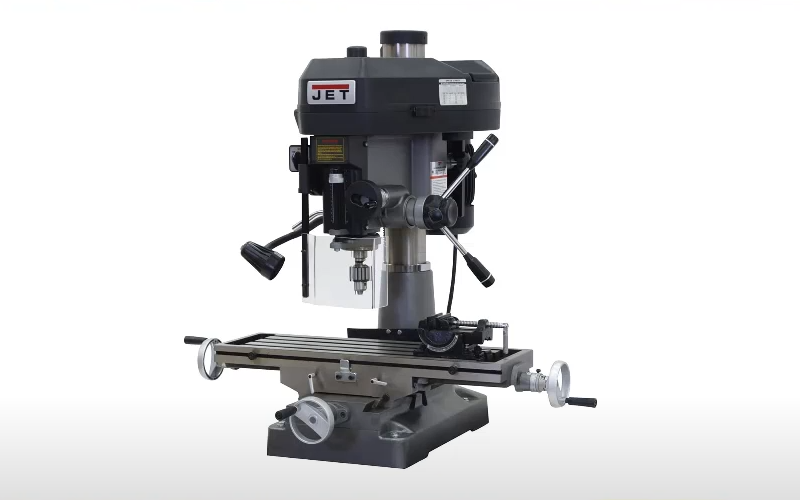
One essential aspect to take into consideration in CNC milling is worldly compatibility. Depending on the kind of material being machined, specifications such as reducing rate, feed price, and device selection may need to be changed as necessary. Soft products like plastics can often be machined at higher rates contrasted to tougher products like steel, which require slower speeds and more robust tooling. Comprehending the buildings of the material, including its hardness, machinability, and thermal conductivity, enables operators to enhance the milling process and attain premium outcomes while decreasing wear and tear on tools.
Beyond the technical factors like layout, tooling, and products, there are added factors to consider for maximizing CNC milling procedures. Using sophisticated functions such as toolpath optimization techniques can streamline the milling procedure better, making it possible for quicker machining cycles and minimizing waste.
Furthermore, one of the significant benefits of CNC milling is the capacity to automate repeated tasks, which minimizes human mistake and improves production consistency. While conventional milling machines call for a proficient operator to oversee the manufacturing procedure, CNC milling machines can run neglected, carrying out pre-programmed instructions with accuracy. This degree of automation not only boosts effectiveness but additionally frees up skilled employees from mundane jobs, enabling them to concentrate on better activities such as top quality control and process improvement.
Regardless of its benefits, transitioning to CNC milling is not without obstacles. Preliminary financial investment can be substantial, with expenses connected with obtaining CNC machines, software program, and skilled employees training. Nevertheless, many services find that the long-lasting savings connected with increased efficiency, reduced product waste, and enhanced item quality surpass the initial prices. The schedule of renting options and budget friendly entry-level CNC milling machines has made it extra available for mid-sized and tiny companies to adopt this innovation.
Training and skill advancement for employees operating CNC milling devices are likewise crucial for taking full advantage of the return on financial investment. Operators need a strong understanding of both the CNC maker itself and the software program being used for programming and tracking. Lots of suppliers find success by providing in-house training programs or partnering with outside training companies to outfit their groups with the necessary skills and understanding.
In recent years, technical advancements proceed to form the area of CNC milling. As markets progressively transform to automation, integrating functions such as synthetic intelligence (AI) and device knowing into CNC machines can further improve the accuracy and performance of milling procedures.
Additionally, improvements in software application are constantly narrowing the void in between style and production. Modern CAD/CAM systems now provide more instinctive user interfaces and enhanced simulation abilities, allowing drivers to envision machining procedures before they are performed. By spotting potential concerns in the style phase, firms can solve design flaws or maximize reducing techniques without incurring pricey modifications to physical products.
In the context of CNC milling, sustainability is likewise obtaining value as producers look for means to minimize their environmental impact. Applying methods such as optimizing reducing criteria, utilizing much more efficient tooling, and reusing materials can add to a much more sustainable milling procedure. Furthermore, technologies such as additive production are being checked out along with CNC milling, providing opportunities for hybrid production methods that further boost sustainability by reducing waste.
Explore benchtop milling machine the transformative globe of CNC milling, a technology that incorporates precision and automation to produce top notch elements successfully from different materials, and find its processes, benefits, and crucial considerations for success in modern-day manufacturing.
In final thought, CNC milling stands for a crucial asset in modern manufacturing, supplying firms with the capacity to generate complex and top quality elements effectively. Recognizing CNC milling starts with a solid structure in its processes, including the interplay between design, tooling, materials, and software application. Eventually, effective assimilation of CNC milling equipment, skilled workforce training, and smart automation paves the way for the future of manufacturing, where effectiveness, sustainability, and high quality become the hallmarks of operational excellence.